Do-it-yourself restoration: Reproducing parts
What to do when you need a part that isn’t available
What do you do when you can’t find a part? If you’re Dennis Bickford, you make it yourself. When that’s not possible, Bickford teams up with those with the equipment to make the parts he and his customers need. And he’ll be the first person to say, “You can, too.”
Along with his wife Kathy, Bickford owns Vintage Woodworks, a restoration shop with work previously featured in Old Cars Guide to Auto Restoration. Vintage Woodworks completes many aspects of restoration, but in its 35 years, the business has evolved to focus on wood and upholstery in Chrysler Town and Country models from the 1940s. However, the process for reproducing out-of-production parts to be covered here extends beyond those dazzling wood-bodied cars to any type of automobile with rubber components.
The part to be reproduced here is a rubber sill mat for 1942-’48 Dodge, De Soto and Chrysler convertible and two-door coupes, and is only visible when the door is opened. There are essentially two parts to these sill mats: a metal base and the rubber that forms around it. In the six decades or so since Chrysler Corp. built these mats, the rubber has cracked and the metal bases have rusted. As as result, those mats that have survived are not up to the aesthetic standards of a freshly veneered Town and Country, nor are they up the functional standards of a Dodge or De Soto coupe or convertible that is driven.
To begin reproducing a component, Bickford breaks it down into its parts. In this instance, he started with the metal core, which was essentially made from sheet metal upon which the factory welded studs. Using an original core as a template, a new core was cut in the proper shape from sheet metal and studs exactly like the originals were welded on, then the whole part was powder coated.
Bickford does not maintain the equipment to mold rubber, but word of mouth has led him to someone with this capability. Even though Bickford operates in central Wisconsin, a very rural area, he found someone with such skills within 10 miles of his door. Jeff Weisbrod of Weisbrod Model and Machine makes relatively small runs of parts for medical and furniture companies, computer companies and other businesses, such as Vintage Woodworks. He equates the process of reproducing this sill mat to rapid prototyping (the automatic construction of physical objects using additive manufacturing technology). Best of all, he’s able to produce the tooling and part at a reasonable cost that justifies small runs, such as those in the restoration of cars less common than 1957 Chevrolets and two-seat Thunderbirds.
“It’s probably the least expensive way to get tooling, but it’s also durable and you still have the masters — the original part still exists,” Weisbrod said.
At this point, Bickford passes the reproduction process over to Weisbrod. His first step to reproducing the rubber portion of the sill mat is repairing an original mat. Bickford presented the best original mats he could to Weisbrod (one for each side), and Weisbrod repaired them by filling in the cracks and replacing any chunks of rubber that may have been missing. The goal was to have a part that looked OEM, and any flaws in the original will be duplicated in the reproduction process. Therefore, these flaws must be eliminated.
Once the original part’s surface has been restored as new as possible, it can be used to make the tooling. In this instance, Weisbrod placed the original mat in an aluminum frame to hold it in place, then poured a two-part castable material over the part. The original part can be removed once the mold hardens. A mix of a special urethane can be poured into this mold to create the new sill mat. The urethane can be whatever color is desired, but in this case, a simple black is used to replicate the original rubber mat.
Although these steps are specific to one part, they can be followed to reproduce or create an infinite number of other parts. If a source for mats, trim, upholstery or any other item does not offer the part you need, contact them about reproducing the part. Or, work with someone like Weisbrod to make the parts you need. You may end up starting a new business.
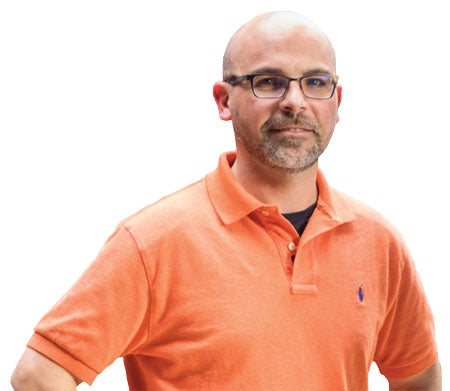
Angelo Van Bogart is the editor of Old Cars magazine and wrote the column "Hot Wheels Hunting" for Toy Cars & Models magazine for several years. He has authored several books including "Hot Wheels 40 Years," "Hot Wheels Classics: The Redline Era" and "Cadillac: 100 Years of Innovation." His 2023 book "Inside the Duesenberg SSJ" is his latest. He can be reached at avanbogart@aimmedia.com